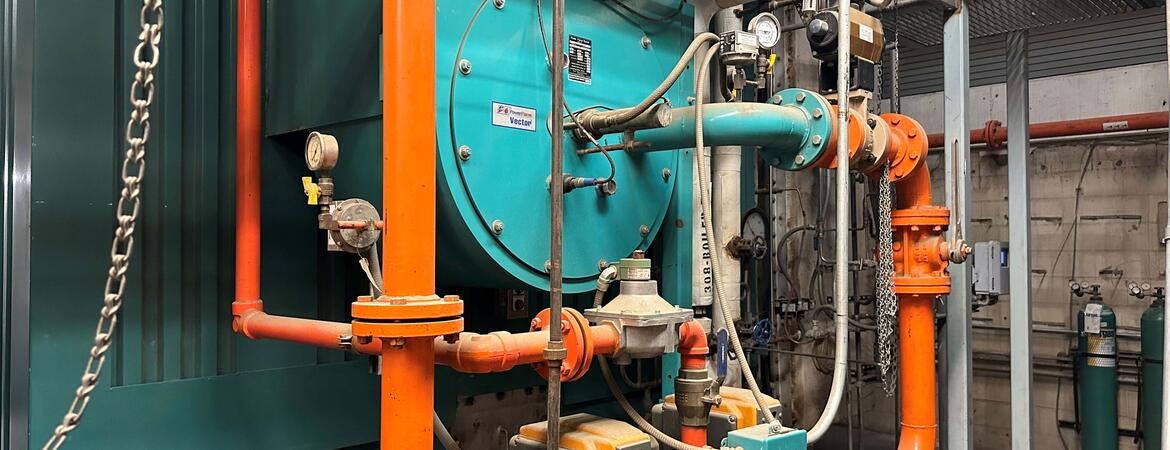
Just before sunrise on July 15, teams of skilled-trade staff met at UCR’s Central Plant to begin the process of shutting down the central boilers and draining the steam condensate lines. This quickly raised working conditions at the plant to 120-130 degrees, as hot as Death Valley. They were prepared with heat illness training and electrolyte water.
Pressurized steam would be offline for nine days to make routine repairs and upgrades. However, with annual steam shutdowns suspended since June 2019, due to COVID-19, there was extensive work to do.
“An inspection had identified 214 failed steam traps,” Bill Hensche, building mechanical/HVAC-R supervisor, said. A 40-foot section of a 5” steam-condensate line needed replacing. There were also five, 8” steam valves failing, which are used for isolating campus buildings independently. The FS project management team facilitated with securing contractors for the operation.
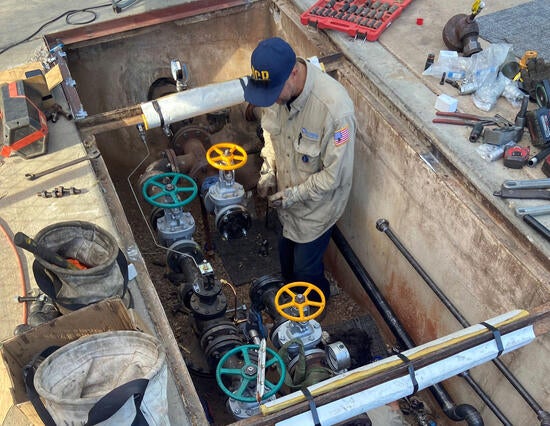
(UCR/Bill Hensche)
After working nonstop for two days, in 10-12 hour shifts, the steam condensate lines were drained and working conditions lowered to outdoor temperatures.
Repairs followed. In groups, staff continued working 24 hours a day, with some working 12-14 days consecutively.
The abatement team removed several sections of pipe insulation and pipe flange gaskets in mechanical rooms and tunnels. They stayed on standby, ready to mobilize for any new abatement issues for the duration of the shutdown.
The sheet metal shop fabricated and welded several sections into place of compromised steam and steam condensate piping.
The plumbing shop assisted the building mechanical team with the initial drain down, steam trap-set fabrication and installation, and bringing the steam back up.
Central Plant balanced cleaning and inspecting boilers and repairing steam valves with providing operators for the chilled water plant.
The process of changing out steam traps and installing a new condensate pump station took place in vault 31. There was a complete rebuild of the street vault outside of the steam plant. Contractors installed 15 drip legs for the high-pressure steam condensate return line from vault 6-18.
A condensate return system collects and transports water from the steam system back to the boiler. When a failing pipe is full of water, steam is unable to press through.
On July 23, staff worked a nearly 15-hour shift to bring steam online to all campus buildings. By the end, Central Plant had also replaced its outdated continuous emissions monitors— hefty equipment which ensures UCR stays within South Coast Air Quality Management District, or AQMD, rules and standards for reduction of greenhouse gas emissions.
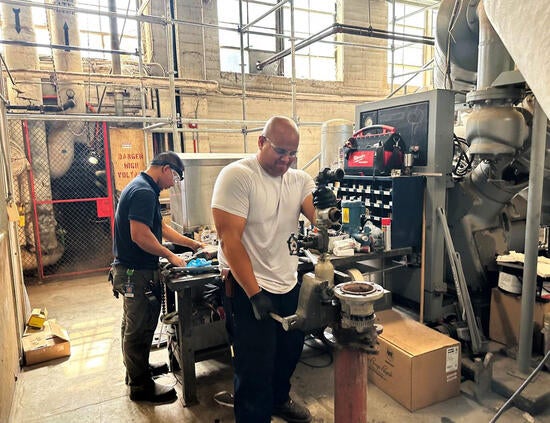
“Each boiler is required to have one of these units to comply with AQMD,” Nils Burkland, central plant supervisor, said. “Our old system was obsolete.” With four boilers, the installation cost a substantial sum.
Various employees worked together on the massive effort— Central Plant, Energy & Engineering, plumbing, abatement, building mechanical, HVAC, carpentry, sheet metal, project management, purchasing, and some general contractors.
Environmental Health & Safety pulled air samples and performed testing for safety measures to ensure no one was being placed in harm’s way.
FS’s purchasing team rushed purchase orders and made themselves available for orders during the shutdown, all while using a new financial system from Impact 23.
The Energy and Engineering team helped to ensure the steam trap work and documentation would meet qualifications for energy efficiency rebate incentives from SoCal Gas.
The School of Business was even able to take advantage of the shutdown to perform work for their new building project, which saved the campus an additional outage.
“Looking ahead, we will have some sections of the pipe re-insulated by the contractor to help with keeping the heat down in the tunnels,” Hensche said.
As a supervisor on the project, Hensche said he had to recognize, “the dedication and hard work, through the long hours and continuous back-to-back days, of FS employees who were involved and the other departments that assisted.”
Pressurized steam supply is critical for lab sterilization, hot water, and maintaining building climates. Annual steam shutdowns help limit unplanned failures in the steam distribution system.